A Visit to the Central Virginia Fiber Mill

Last month on our way to Laughing Sheep Yarns in Charlottesville, VA for our Trunk Show we took a detour to visit our friend Mary Kearney at Central Virginia Fiber Mill in Ruckersville, VA. Mary gave us a tour of the mill and we discussed various aspects of running the fiber mill.
The tour began at the skirting table. This is the first stop on the fiber's journey, once it arrives and is unpacked. Here, the fleece is laid out and undesirable parts are removed. These include things like vegetable matter, tags (manure and sweat locks), other debris and foreign objects. The staple length is checked to ensure the mill can process it.
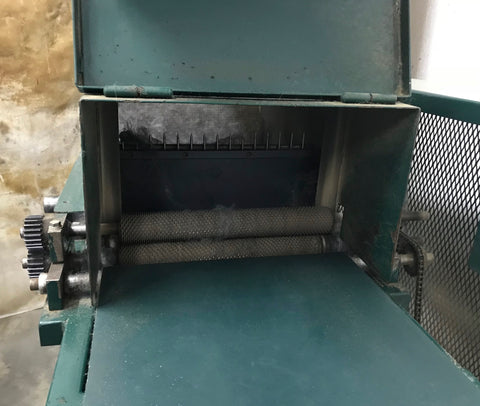
We stopped here to discuss the types of fiber that get processed at the mill. Although the mills main focus used to be alpaca, at this time they process alpaca, wool, and llama fleeces. To go all the way to being spun into yarn, the staple length of the fiber must be at least 3-3.5 inches, otherwise it can only go through the process of becoming roving or a batt.
Once all the bad parts are removed through skirting, the fleece is taken over the the washing station. Here Mary uses a series of hot water baths in conjunction with an eco-friendly scour agent to remove dust, dirt, clay, and lanolin from the fleece. Then the fleece is laid out to dry.
Once the fleece is dry, it then comes over to the picker. The picker pulls apart the tangled fibers and provides better consistency in later processing. The picker blows the picked fibers into a collection room. Conditioning oils may be applied in this process to cut down on static electricity. For finer fibers, Mary offers a hand picking service at additional cost.
Once the fiber has been teased open, it is ready to go to the carder. Here the fiber is further separated out by passing on and off a series of rollers (4 sets of two) covered in carding cloth. The fiber will be rolled on and off the different drums passing through different sized teeth pointing in different directions. The final product of the carder is either roving or batts.
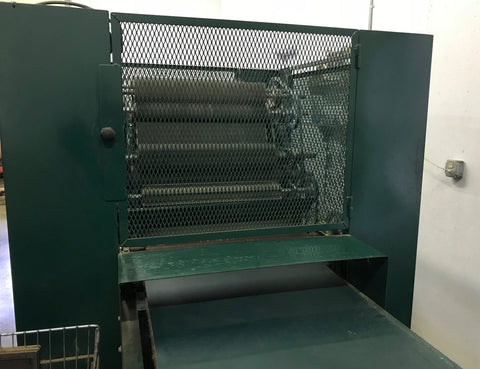
Here the fiber journey hits a fork in the road. Both the batts and roving are suitable for projects like hand spinning and felting. If these are the intended uses, the fiber has reached the end of it’s journey and will be packed up and sent back to it’s owner. However there are additional services available at the mill. Batts can go to the wet felting machine to be made into felt sheets for a cornucopia of projects. The roving can continue it’s journey to be further processed into spun yarn.
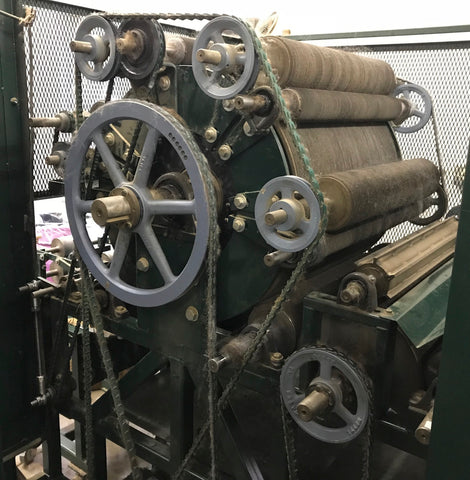
To go from roving to spun yarn, the fiber must first be drawn out. This happens in the pin drafter (also called a draw frame or gill box). The roving (or sliver) that came from the carder is passed through the pin drafter which will even out the roving. At this stage, multiple rovings can be drawn together to blend them. The fiber may be passed through the pin drafter multiple times to ensure it is even and ready to be passed through to the spinning frame. The end product is a more uniform and longer roving. Typically the roving comes out 3 times longer each time it is ran through the machine.
Spinning the roving into yarn still takes a few steps. The roving itself is spun into a single ply yarn. Once that step is completed, between two and four singles are then plied together to create the finished yarn. At Central Virginia Fiber Mill, the machine that does the spinning is the same machine that does the plying. The singles are spun on one side of the machine, and the plying is done on the other side.
Once the yarn has been spun, you can have it put up in hanks (sometimes called "skeins" by dyers and hobbyists) or on cones. Now the yarn is ready to be sent back to it’s owner and enjoyed!
Here are some of the questions we asked while we were touring the mill:
The Fiberists: How did you get into owning and running a fiber mill?
Mary: I started when I watched a woman spinning from a bunny at a fiber festival. This lead to owning and spinning from angora bunnies. Then I wanted something to blend in, which lead to angora goats to blend in with the bunny fiber. This then lead to alpacas and having too much fiber on hand.
When I sent the fiber to a mill, I didn’t get my own fiber back, just an equivalent amount of fiber, this bothered me because I spend a lot of time and effort to raise an animal and harvest their fleece, I wanted to get that specific fleece back. At the time there was no one in Virginia doing fiber processing. I did the research and found that there was a need for small farm fiber processing so that you could guarantee that you would get your fiber back.
TF: What is the oddest thing you have found while skirting a fleece?
This is the obvious reason why it is called a “Pin Drafter”
M: Because animals are often vaccinated at the same time they are sheered, sometimes the syringes get mixed in with the fleece. I once found a doffer brush. Other things I've found occasionally are tooth and nail fragments from grooming being done at the same time as sheering.
TF: What is some of the nicest fiber to have come through the mill?
M: Corridale and Romnydale
TF: What is your favorite part about running the mill?
M: The satisfaction on people’s faces when they can see their animal’s fiber made into a finished product.
TF: What part of running the mill do you hate?
M: Having to let people know that the fiber they sent me is of low quality and that it can’t be processed.
A view of the bobbins where spun yarn is collected. The opposite side of the machine is used for plying.
TF: What kind of milling equipment do you use?
M: We have Stonehedge Fiber Milling Equipment (For more information you can see their website here: http://fibermillingequipment.com/). This includes the picker, carder, spinner/plyer, and skein winder. The pin drafter was rebuilt and refurbished from another fiber mill.
TF: Do you steam the yarns to finish them?
M: No, we focus on creating a balanced yarn, so there is no need to use steam to even the yarn out.
Additional Information:
Quick visual summary of the process of milling fiber: http://www.ramella.com/process.php
Tips for sending fiber to a mill to be processed:
Meet with the mill owners
- Discuss what services they offer and the estimated costs
- Make sure they are knowledgeable about the process and that they can provide you the right level of service
Keep a small amount of the unprocessed fiber
- Fiber processing is laborious and can take months before your fiber is sent back
- Keeping a small sample will allow you to compare and verify what you received is what you sent
Pre Skirt your fleece
- A lot of mill services are based on incoming weight, so the more unusable parts your remove, the less you will pay
- Additional fees will be charged to re-skirt a bad fleece
Pre-Wash your fleece
- Washing your fleece before sending it to the mill removes dirt and lanolin, both of which could account for 10% or more of the weight of the fleece
- You can buy scouring agents like Kookaburra Scour to help with the removal of lanolin and sweat from your fleece